Max has been at the heart of women’s wardrobes for over 40 years. As a go-to lifestyle destination, we’ve had your back, literally. Mindfully designed, easy to wear, and even kinder on Mother Earth, life moves fast and we’re here to make sure your wardrobe keeps up. Our timeless and feel-good wardrobe favourites aren’t just here for today— they’re ready for all your tomorrows. Made in premium fabrics that age like a fine wine, being fashionably late never looked this good.
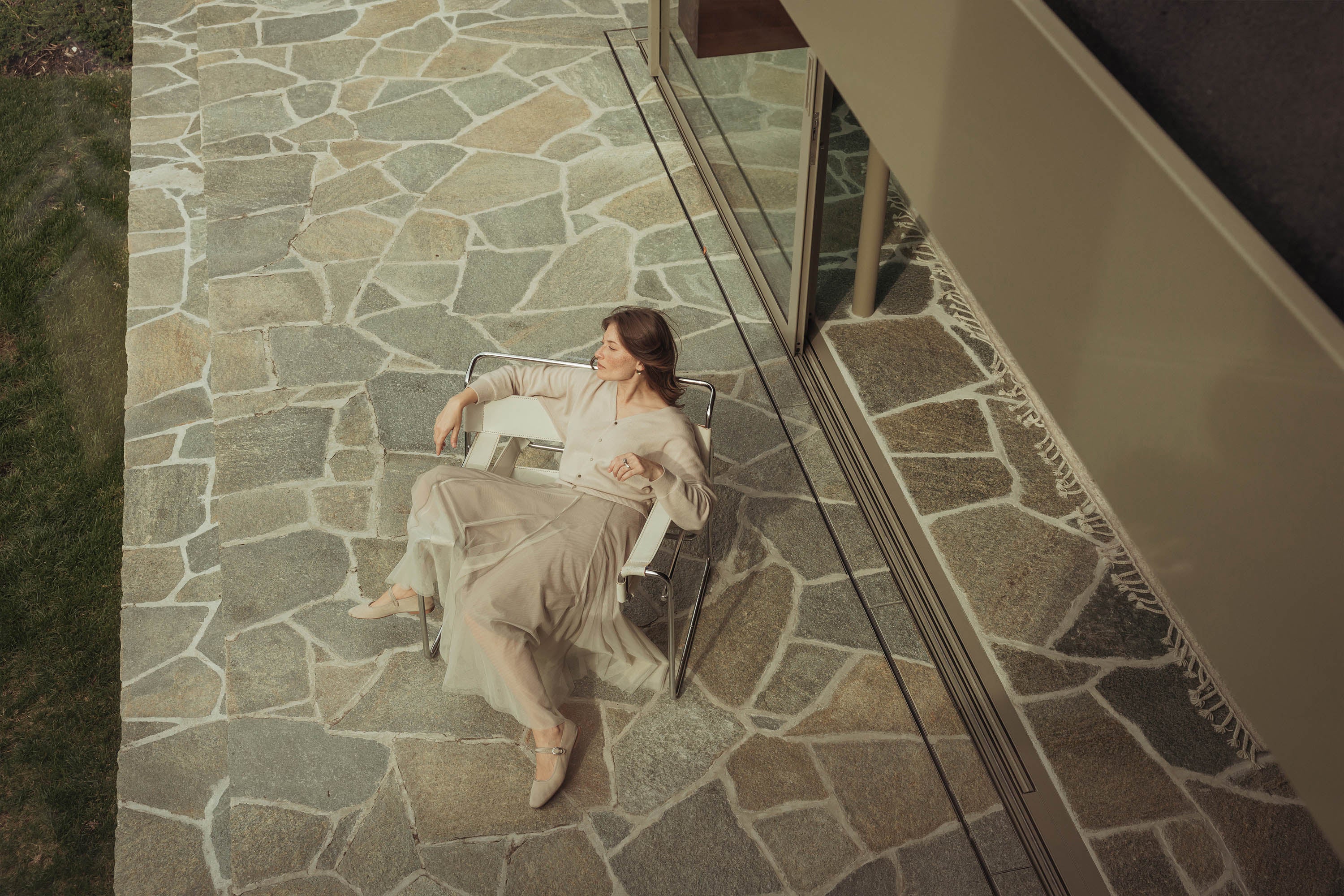

We mean business and not the boring kind. The kind that looks good, feels better and works as hard as you do. We’re talking premium fabrics and pieces made to wear now and love forever: like Max Denim, made in the world’s cleanest denim factory, and traceable ZQRX merino straight from New Zealand farms. But we’re not just a pretty face, we’re serious about sustainability too. That means friendlier fabrics, recycled materials, and factories that care as much we do. You’ve got standards, and we do too.
Because at the end of the day, our purpose is simple: to make getting dressed the easiest (and best) part of your day.
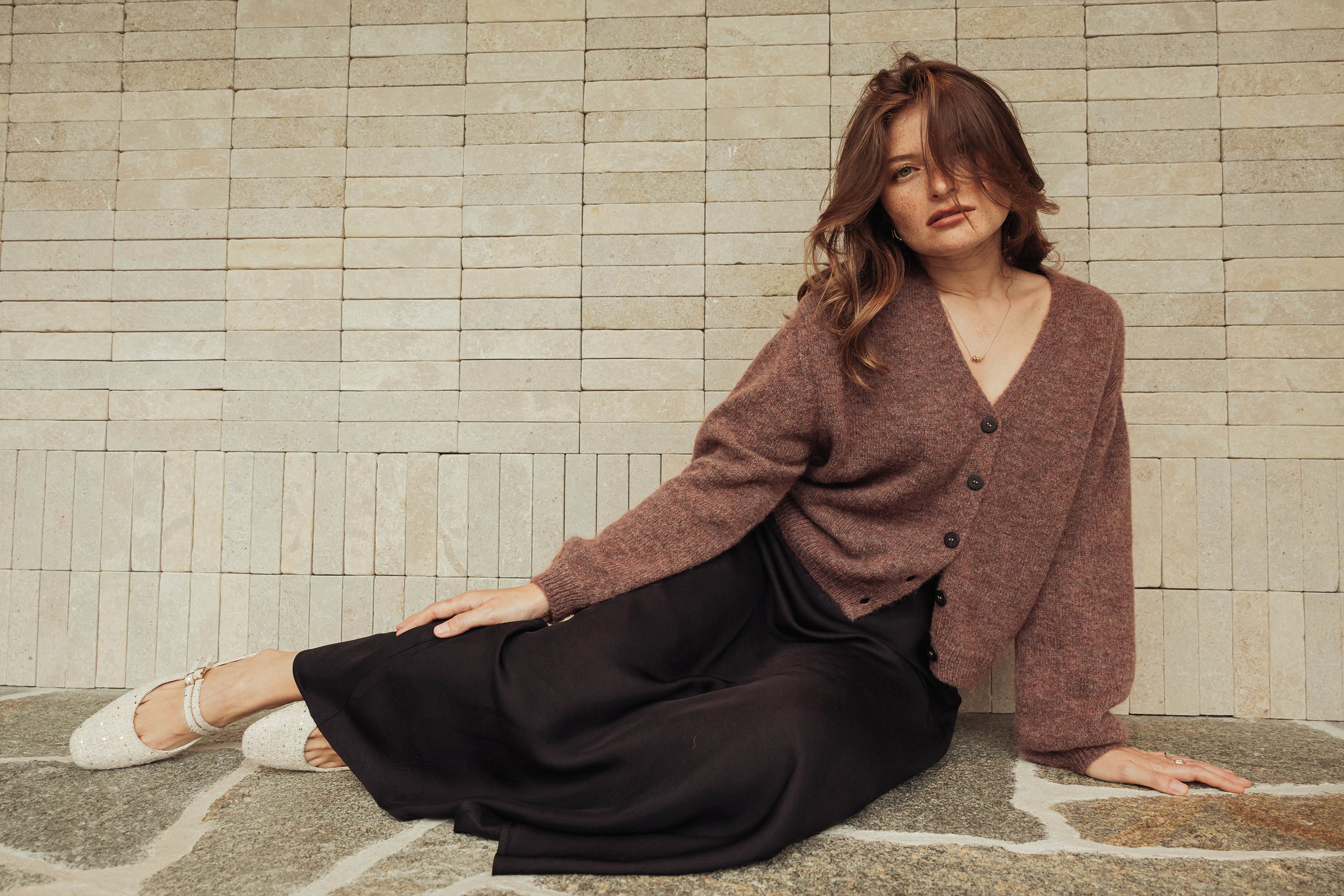
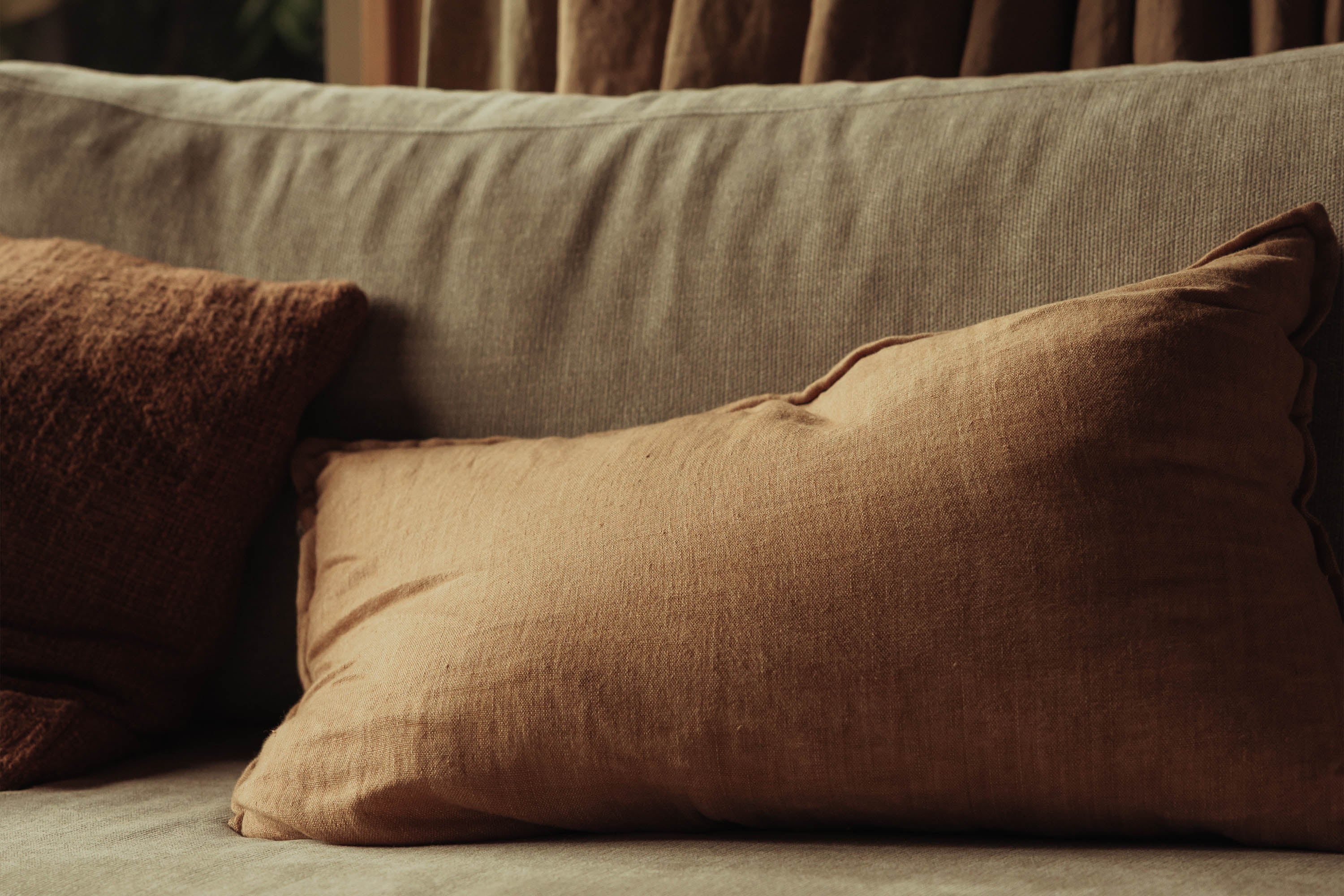
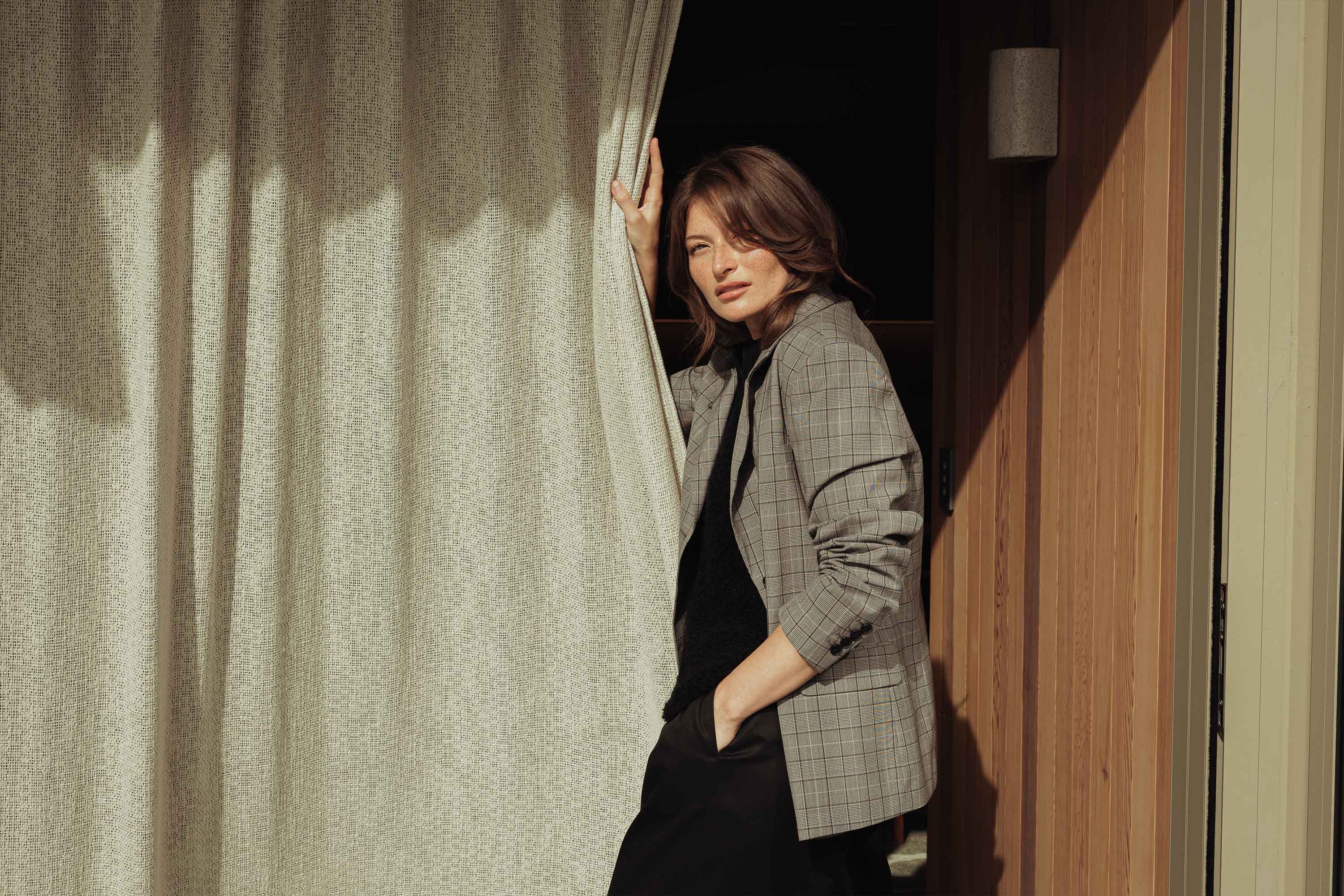